靴の製造現場in株式会社アサヒコーポレーション
普段、皆さまがほとんど毎日履いているシューズは
どのようにして出来ているかご存知ですか??
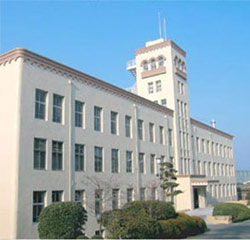
福岡県久留米市に本社がある株式会社アサヒコーポレーションさんに
お邪魔して靴が出来る工程を見学させていただきました。
それでは、ワクワクの工場見学へ出発だ!!!
設計の工程
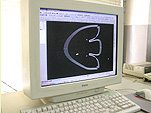
昔はシューズの設計図も設計者さん達の一つ一つ手書きで行っていましたが、
現在はPCのCAD(コンピュータ支援設計システム)を活用して、
シューズの各部品や仕上がりの図面まで全て作成する事が出来ます。
(紳士靴の場合、20部品以上のパーツで形成されています)
CADを使う事により以前の手作業で行っていた時よりも精度とスピードが上がり、
大変効率よく生産者の手助けが出来ています。
ゴム練り・生地裁断の工程
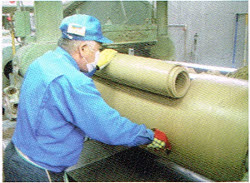
靴底の原料となるゴムをローラーで練り上げていきます。
練り上げる工程も同じ作業を複数回繰り返して板状にします。
・天然ゴム(ゴム樹脂から出る分泌液を固まらせて作った天然のゴム)

アサヒコーポレーションさんは、タイ・インドネシア・マレーシア等の
諸外国から輸入。
・合成ゴム(人工的に石油から作った化学製のゴム)
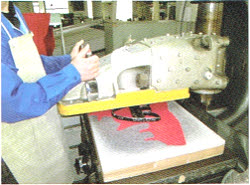
アッパーの材料となる生地を貼り合わせたものや革などを
裁断機で一つ一つ決められた形に裁断していきます。
ゴム成形・生地縫製の工程
板状になったゴムを四角形の1枚のパーツに裁断して、
金型に入れた後に、熱を加えながらプレス機でプレスしていきます。
このとき、約10分程度一定の圧力でゴムを伸ばして成形します。
成形の終わったゴムはバリ(はみ出し部)を取り除きます。
↓
靴底の完成
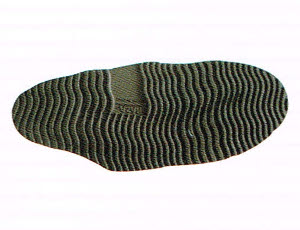
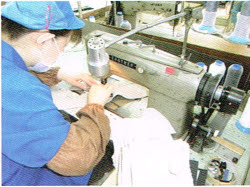
裁断機で裁断された生地は、一つ一つ手作業で
ミシンを使いながら裁断同様決められた形になるように縫製します。
↓
アッパーの完成
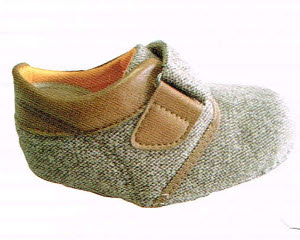
加工・吊込みの工程
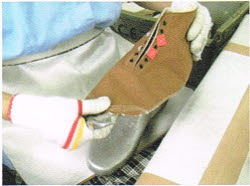
流れ作業で、職人さん達がパーツをつけて加工していきます。
私たちの足の形で作られた足型にアッパーを被せて、
靴底にのりをつけてアッパーと接着をしていきます。
このときの、のりの量やのりを付ける場所は長年培われた
職人さんにしか出来ない経験を元にした勘で行われます。
加硫(かりゅう)の工程
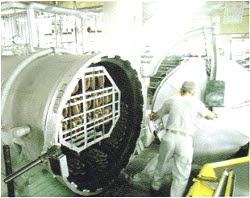
アッパーと靴底が一つになったものを、一定量吊るして
釜に入れて、釜の中で硫黄と熱を加えゴムに弾力性を出させます。
勿論、靴の種類・サイズによって釜に入れる時間は違ってきます。
アサヒコーポレーションさんの釜は、1回で200〜300足が投入でき、
釜の大きさは直径1.7m×長さ6mもある大きな釜です。
仕上の工程

加硫でゴムに弾力性が出たシューズはいよいよ最終工程に入ります。
レーンの上を流れてきたシューズは針などの不純物が入っていないか
チェックするため検針機を通って、シューズペーパーで梱包して
アサヒコーポレーションさん専用の化粧箱に入れられて完成します。
完成したシューズは全国の小売店さんやデパートなどにお届けされます。
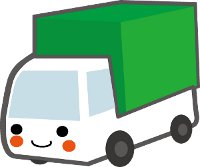
(アサヒコーポレーションさんの2011年の年間国内生産は400万足でした)
工場見学は、どうでしたか??
一つのシューズを作るのに設計を担当されている方から、
製造の職人さんまで様々な人の手を通って
皆さまの足元へとやってきているのが分かりましたね。

今の時代は国外から大量&安価で様々な商品が日本に入ってきます。
アサヒコーポレーションさんでも以前は日本の国内工場で
ほとんどの靴の全工程を作られていたようですが、
今では全生産比率の国内に占める割合は40%弱だそうです。
この数字は国内のシューズメーカーさんの中では非常に大きく
当店でも、アサヒコーポレーションさんを始めとしたメーカーさんの
シューズを様々取り扱わせていただいておりますので、
皆さまにシューズ製作に関わった全ての人の気持ちを
当店の感謝の気持ちに添えてお届けさせていただきます。
どのようにして出来ているかご存知ですか??
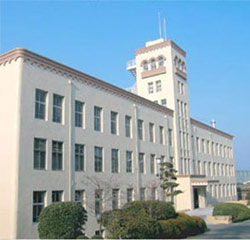
福岡県久留米市に本社がある株式会社アサヒコーポレーションさんに
お邪魔して靴が出来る工程を見学させていただきました。
それでは、ワクワクの工場見学へ出発だ!!!

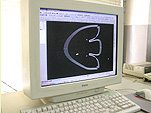
昔はシューズの設計図も設計者さん達の一つ一つ手書きで行っていましたが、
現在はPCのCAD(コンピュータ支援設計システム)を活用して、
シューズの各部品や仕上がりの図面まで全て作成する事が出来ます。
(紳士靴の場合、20部品以上のパーツで形成されています)
CADを使う事により以前の手作業で行っていた時よりも精度とスピードが上がり、
大変効率よく生産者の手助けが出来ています。

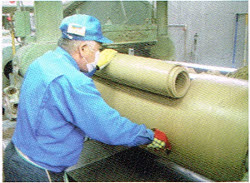
靴底の原料となるゴムをローラーで練り上げていきます。
練り上げる工程も同じ作業を複数回繰り返して板状にします。
・天然ゴム(ゴム樹脂から出る分泌液を固まらせて作った天然のゴム)

アサヒコーポレーションさんは、タイ・インドネシア・マレーシア等の
諸外国から輸入。
・合成ゴム(人工的に石油から作った化学製のゴム)
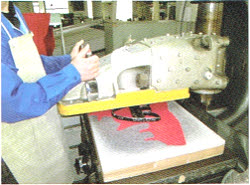
アッパーの材料となる生地を貼り合わせたものや革などを
裁断機で一つ一つ決められた形に裁断していきます。

板状になったゴムを四角形の1枚のパーツに裁断して、
金型に入れた後に、熱を加えながらプレス機でプレスしていきます。
このとき、約10分程度一定の圧力でゴムを伸ばして成形します。
成形の終わったゴムはバリ(はみ出し部)を取り除きます。
↓
靴底の完成
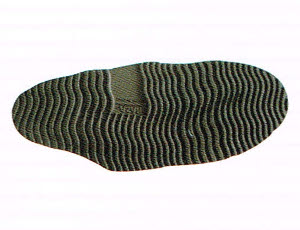
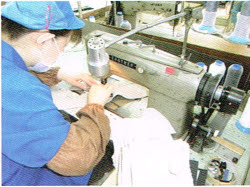
裁断機で裁断された生地は、一つ一つ手作業で
ミシンを使いながら裁断同様決められた形になるように縫製します。
↓
アッパーの完成
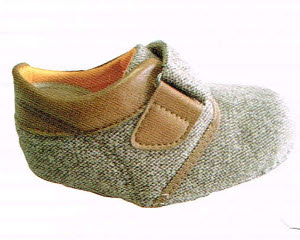

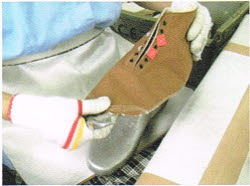
流れ作業で、職人さん達がパーツをつけて加工していきます。
私たちの足の形で作られた足型にアッパーを被せて、
靴底にのりをつけてアッパーと接着をしていきます。
このときの、のりの量やのりを付ける場所は長年培われた
職人さんにしか出来ない経験を元にした勘で行われます。

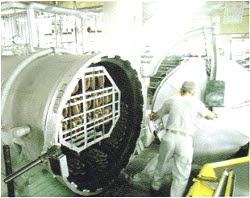
アッパーと靴底が一つになったものを、一定量吊るして
釜に入れて、釜の中で硫黄と熱を加えゴムに弾力性を出させます。
勿論、靴の種類・サイズによって釜に入れる時間は違ってきます。
アサヒコーポレーションさんの釜は、1回で200〜300足が投入でき、
釜の大きさは直径1.7m×長さ6mもある大きな釜です。


加硫でゴムに弾力性が出たシューズはいよいよ最終工程に入ります。
レーンの上を流れてきたシューズは針などの不純物が入っていないか
チェックするため検針機を通って、シューズペーパーで梱包して
アサヒコーポレーションさん専用の化粧箱に入れられて完成します。
完成したシューズは全国の小売店さんやデパートなどにお届けされます。
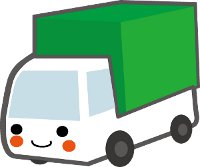
(アサヒコーポレーションさんの2011年の年間国内生産は400万足でした)
※上記の製造方法はバルカナイズ製法です。
工場見学は、どうでしたか??
一つのシューズを作るのに設計を担当されている方から、
製造の職人さんまで様々な人の手を通って
皆さまの足元へとやってきているのが分かりましたね。

今の時代は国外から大量&安価で様々な商品が日本に入ってきます。
アサヒコーポレーションさんでも以前は日本の国内工場で
ほとんどの靴の全工程を作られていたようですが、
今では全生産比率の国内に占める割合は40%弱だそうです。
この数字は国内のシューズメーカーさんの中では非常に大きく
当店でも、アサヒコーポレーションさんを始めとしたメーカーさんの
シューズを様々取り扱わせていただいておりますので、
皆さまにシューズ製作に関わった全ての人の気持ちを
当店の感謝の気持ちに添えてお届けさせていただきます。